Utilities
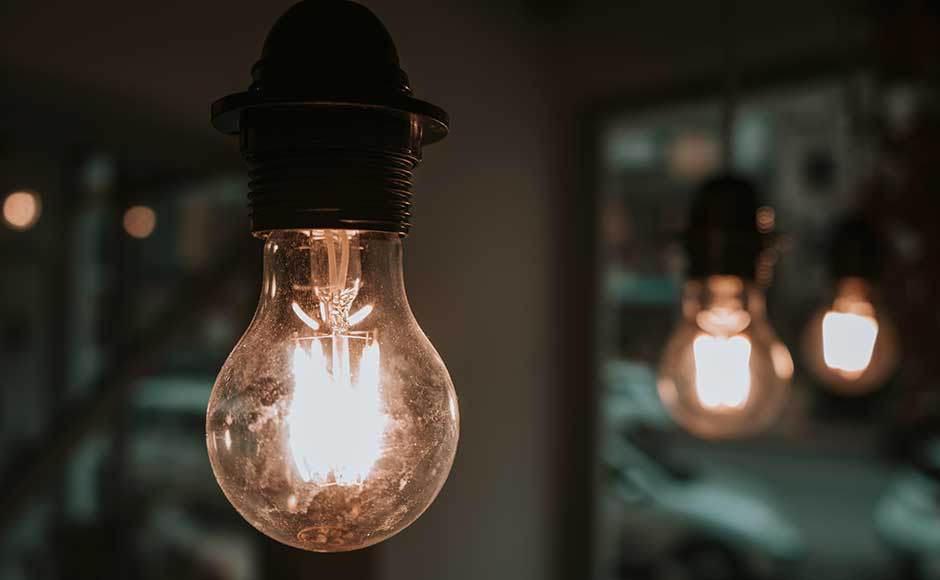
The safe supply and use of utilities (water, gas, oil, and electricity) is important to ensure the safety and welfare of everyone who uses congregational buildings. It is important to follow a suitable system of regular inspection and testing in all buildings and to fix any defects as soon as possible.
It is also important to remember that any insurance policies relevant to properties may be invalidated if utility systems are not maintained and certified to be safe.
Electric supply and equipment
Electrical equipment (portable electrical equipment)
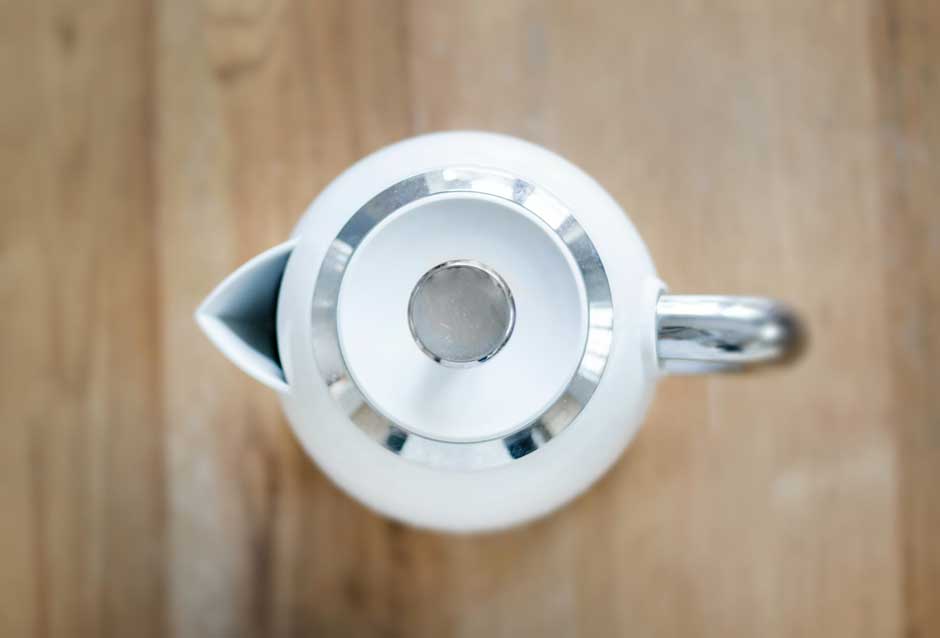
Portable electrical equipment includes kettles, toasters, computers, printers, heaters, organs and radios.
The Health and Safety Executive has a guide to maintaining portable electrical equipment (INDG 236) Please read this fully to develop a system for the inspection and testing of portable electrical equipment, focusing upon the risk of injury.
Not all portable electrical equipment requires an annual Portable Appliance Test (PAT). However, it is necessary to ensure that any electrical equipment purchased or used within church properties is safe to use and suitable for the job intended.
The Church of Scotland General Trustees recommend implementing and recording regular professional PATs and a system of visual inspections of all portable electrical equipment. This should be combined with a formal inspection and testing of portable electrical equipment at an interval relevant to the risk involved. Further advice and guidance can be found by referring to the Health and Safety Executive's guide and from the Church of Scotland General Trustees.
Anyone who carries out PATs must be competent, suitably trained and have the confidence, knowledge and experience to do this safely. Whilst INDG 236 states that an electrician does not need to carry out PATs, the Charity Trustees must be assured that anyone undertaking PATs on their behalf can do so safely and without risk to themselves or anyone else.
It is important to keep suitable and sufficient records of any visual or physical inspection and testing of portable electrical equipment. These records must show who carried out the inspection or testing, as well as the date and location of testing and details of specific pieces of equipment tested and any faults identified. If any action is required – for example, replacing a fuse – this must also be documented and carried out by a competent person.
Electrical safety inspection and certification
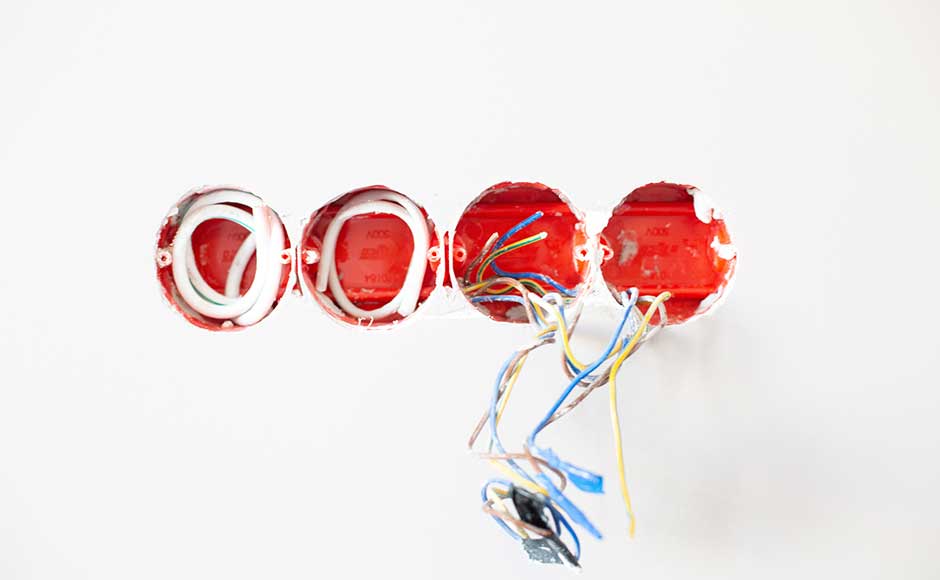
If electrical systems and equipment are not maintained properly, there is a serious risk of injury, burns or fatality from electrical shocks. There is also a substantial risk of electrical fire if electrical systems and equipment are not safe to use.
Electrical safety covers two distinct areas: the electrical supply (fixed system) and the safe use of electrical equipment (including portable electrical equipment).
Fixed wire testing involves testing and inspecting the electrical systems and installations within your associated buildings.
Regular testing of a building’s wiring structure and maintenance is mandatory by law under the Electricity at Work Regulations 1989 and IET Wiring Regulations BS 7671:2008. The Electricity at Work Regulations 1989 apply wherever the Health and Safety at Work Act 1974 applies. These regulations set out, in general terms, the safety requirements for installations and the safety of people working with or near electrical systems. They also impose duties of compliance and, in most cases, these include a duty on the occupier of the premises and a duty on those using the premises.
The Charity Trustees have other legal obligations to consider under the Occupiers Liability Scotland Act 1960 and the Health and Safety at Work Act 1974 to ensure the safety of the general public, congregation and visitors to the church.
Fixed electrical systems must be assessed and tested at least once every five years. Some electrical contractors will allow staggering of testing over the five years so that certain parts of systems are tested annually, adding up to the full assessment over five years. This can be a cost-effective method of ensuring that fixed electrical supplies are safe to use and to ensure that any faults are dealt with as soon as possible.
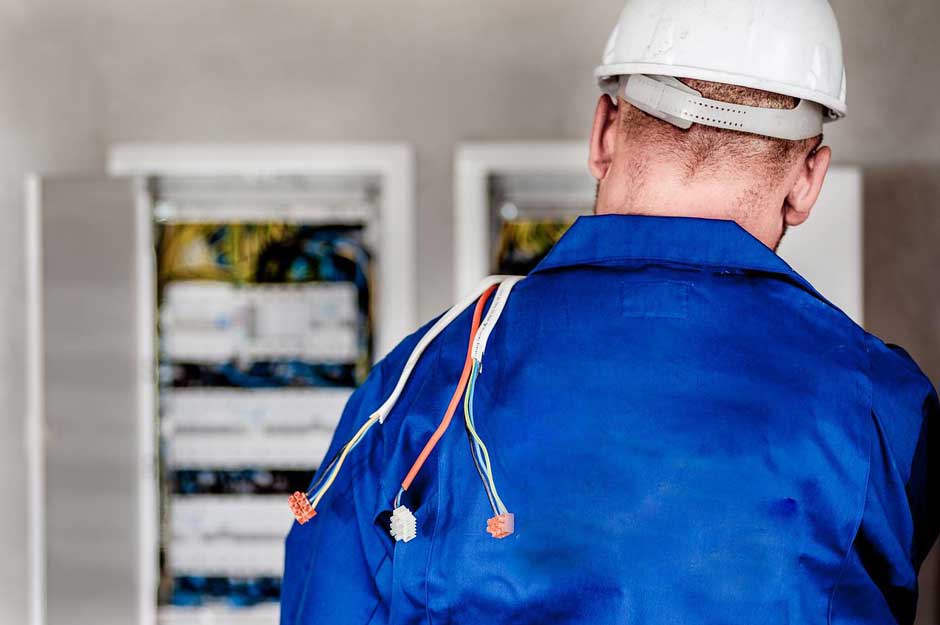
The five-year electrical testing rule applies to churches and associated buildings, including the manses and any privately leased or tenanted properties.
It is a stipulation of most insurance providers, including COSIS, that the five-yearly inspections are carried out due to the associated risk of fire from untested electrical wiring and installations, especially in churches and other historic buildings.
The Charity Trustees must ensure that the five-yearly inspections are carried out and that the electrical systems are deemed safe for use in order to demonstrate ongoing statutory compliance and ensure that the church insurance stipulations have been suitably met.
The Charity Trustees should ensure that they employ a suitably trained and competent electrical engineer who can demonstrate certified competency and relevant public liability and professional indemnity insurance for the works undertaken. The General Trustees and COSIS insurance recommend that the engineers are sourced from a relative industry body that can certify competency and compliance of its members such as SELECT or NIC/EIC.
The General Trustees strongly recommend that the Charity Trustees ensure that any congregational members or friends of the church carrying out these duties are suitably registered with a membership body, professionally insured and can demonstrate the competency required to safely and suitably carry out the inspections and provide the safety certification required. Further advice and guidance is available from the General Trustees, presbytery and COSIS insurance.
Following testing, you will be issued with an Electrical Inspection Condition Report (EICR), certifying the condition of the entire electrical system within your premises, including electrical wiring, circuits, accessories and connections.
Any C1 OR C2 faults identified on the EICR must be rectified to demonstrate compliance with the Electricity at Work Regulations 1998.
Electrical supply (fixed systems)
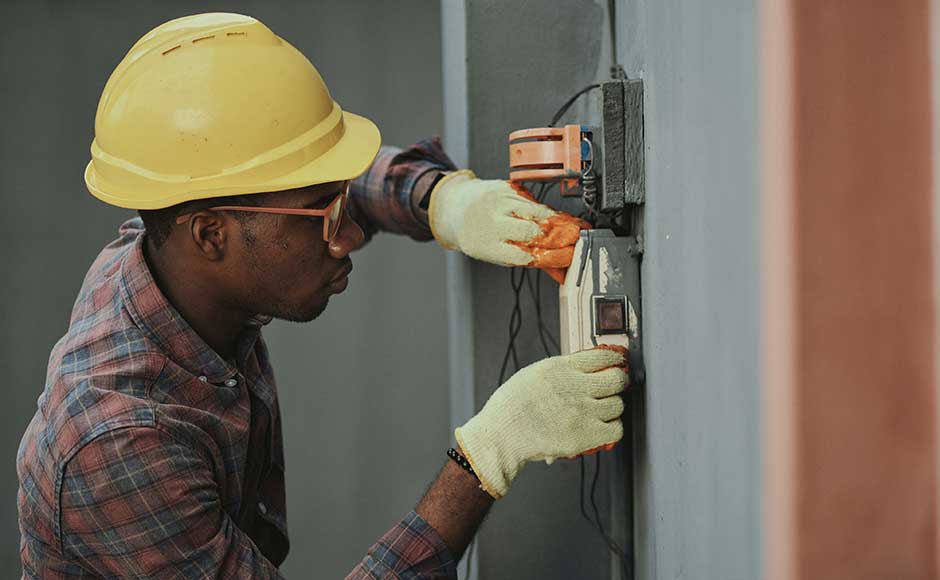
It is necessary to maintain fixed electrical supply systems and to ensure that any faults within these systems are dealt with promptly. The fixed electrical system incorporates the circuits from the meter and consumer unit supplying light switches, sockets and any wired-in equipment such as cookers, dishwashers and washing machines.
It is absolutely vital to carry out regular testing and inspection of your fixed electrical systems. Failing to do so could result in injury, fatality or damage to the building. Failure to undergo regular testing and inspection for long periods of time has also led to some congregations facing costs of tens of thousands of pounds to remedy faults that have been allowed to develop over the years.
The assessment and inspection of the fixed electrical supply is often called a periodic inspection. The periodic inspection will:
- Reveal if any electrical circuits or equipment are overloaded
- Find any potential electric shock risks and fire hazards
- Identify any defective electrical work
- Highlight any lack of earthing or bonding
An Electrical Installation Condition Report (EICR) will be provided, which will identify any of the following: Category 1 (C1, danger present), Category 2 (C2, potentially dangerous), Category 3 (C3, recommendation), or F1 (requires further investigation). Suitable arrangements must be made to correct any C1 or C2 faults without delay.
It is important to retain a copy of the EICR at least until the next periodic inspection is undertaken. It is also necessary to retain all reports and documentation relating to any repairs or upgrading of fixed electrical systems.
Who can carry out the inspection of my fixed electrical system?
Only an appropriately trained and competent electrician may inspect and test fixed electrical systems. It is strongly advised to contact The Electrical Contractors Association of Scotland (SELECT) for advice about appointing an appropriate electrician.
General principles of electrical safety
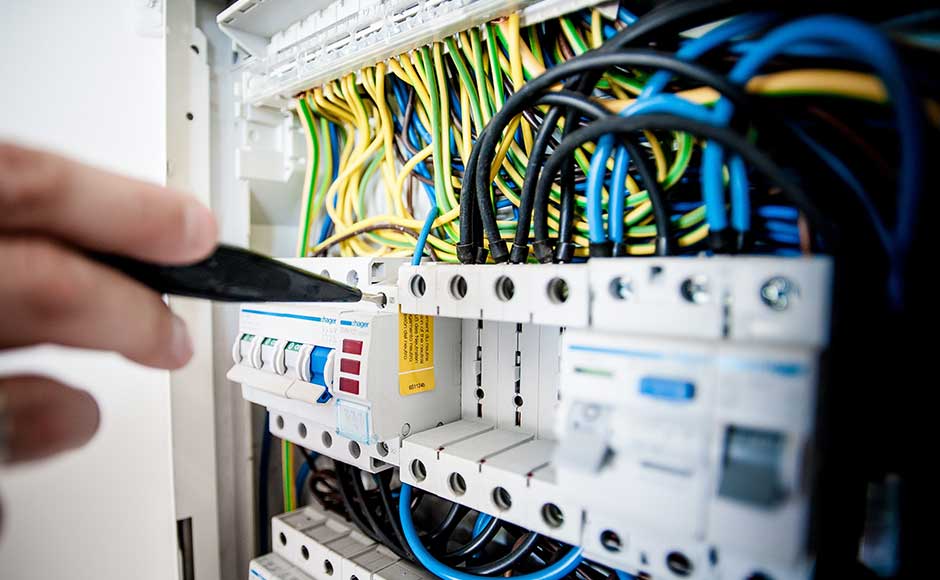
It is important to take positive steps to manage electrical safety, not just to react to accidents or situations as they occur. For example, equipment should not be left until a fault occurs – the aim is to prevent danger. If faults are not found until equipment is to be used, it could be too late to repair or replace it.
It is also important to remember responsibilities under the Management of Health and Safety at Work Regulations (1999) to carry out sufficient risk assessments within properties. This responsibility also extends to all electrical systems and equipment. Please see the risk assessment section for further information.
Although the Electricity at Work Regulations 1989 require that systems (and all equipment) are maintained, the regulations do not explicitly state how often any PAT assessment or testing should be carried out. We recommend all churches perform PAT testing on a regular basis, such as annually.
Gas
Gas safety
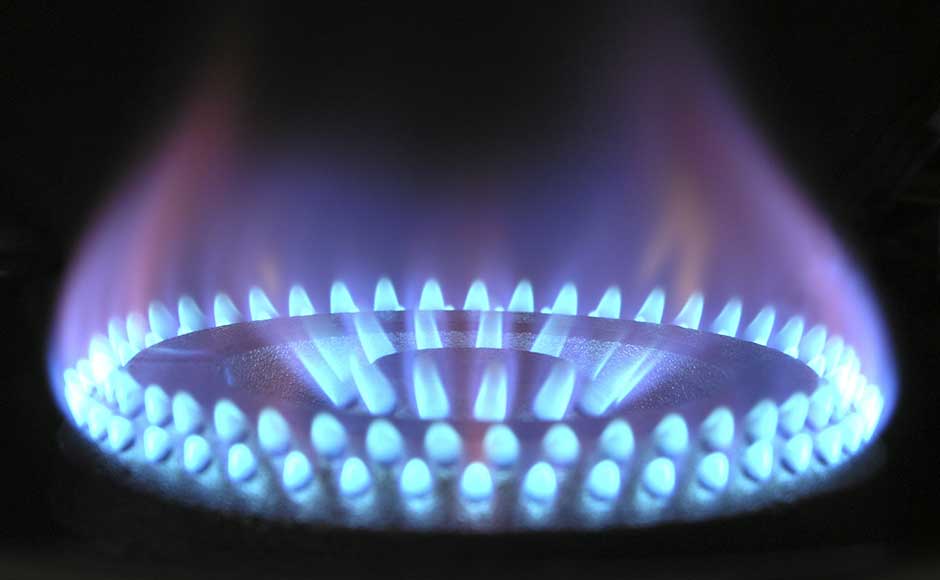
The Gas Safety (Installation and Use) Regulations 1998 require that employers and landlords ensure that any gas appliances and installation pipework installed in properties for which they are responsible are maintained in a safe condition.
The Charity Trustees must also ensure that any gas appliances (including ovens, hobs and boilers) are inspected at least every 12 months by an approved person. The approved person must be a Gas Safe-registered engineer and it is important that their Gas Safe register ID card is checked before any inspection or repair work starts. It is unlawful for anyone other than a Gas Safe engineer to inspect or work on a gas installation, including pipework.
Records must be kept for each appliance to include dates of inspection, defects identified and action taken. These records should be kept in the congregation's property register.
The gas safety checks should not be confused with regular servicing or maintenance schedules. A gas safety check is specifically centred around the safety of the supply, pipework installations, gas pressures and the general safety of the connected appliances. A Gas Safety Certificate will be provided to certify the gas safety at your site in addition to your regular servicing and maintenance. For ease of management, it is recommended that they are both carried out at the same time by the Gas Safe engineer.
Any buildings which have been closed or unoccupied for a period extending 6 months since the last gas safety inspection and in which the gas and associated appliances have not been subject to regular should be deemed safe for use by a registered gas safety engineer before re-instatement and use.
If an appliance is found to be unsafe to use, it is unlawful to use it before suitable repairs are carried out. The Gas Safe engineer will place a prohibition notice on any gas equipment or installation that is unsafe to use and it is illegal to tamper with this notice.
A manse is regarded as domestic premises; therefore, there is no legal obligation to have gas appliances within the manse serviced annually. However, it is strongly recommended that appliances and pipework in the manse be included in the annual gas safety inspection.
If a manse or other residential property is to be let out to tenants, the landlords have a strict responsibility to have gas appliances checked before the lease commences and have these maintained and serviced once a year thereafter. Please seek advice from the Church of Scotland Law Department on all aspects of letting residential property before doing this.
Water
Controlling legionella risk and exposure
The primary method used to control the risk from legionella is water temperature control. Water services should be operated at temperatures that prevent legionella growth:
- Hot water storage cylinders (calorifiers) should store water at 60°C or higher
- Hot water should be distributed at 50°C or higher (thermostatic mixer valves need to be fitted as close as possible to outlets, where a scald risk is identified)
- Cold water should be stored and distributed below 20°C
- A competent person should routinely check, inspect and clean the system, in accordance with the risk assessment.
Where the risk assessment shows that there is a reasonably foreseeable risk of exposure to legionella bacteria, the use of water systems, parts of water systems or systems of work that lead to exposure must be avoided so far as is reasonably practicable.
The congregation’s Health and Safety representative may reasonably conclude that an external water treatment consultant may be required at this stage to take the necessary steps to obtain water samples for legionella analysis. This will determine the bacteria counts and the acceptable levels. Professional cleaning and sterilisation of the water system should then be carried out by professionals and retested to ensure acceptable levels have been restored.
Legionella
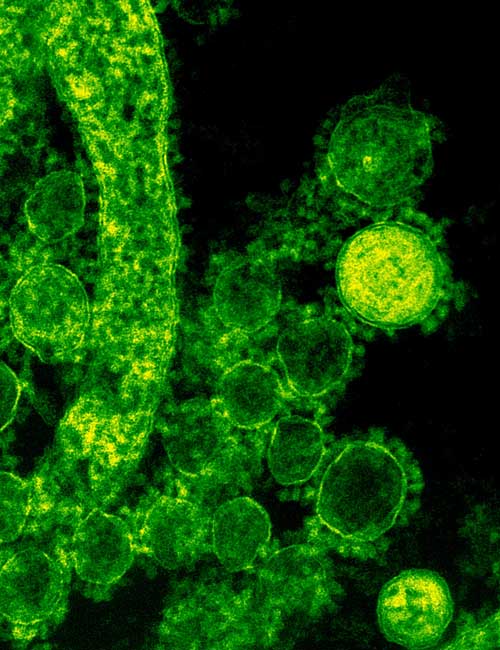
Legionella bacteria are water-loving soil bacteria that are found naturally in the environment. The bacteria are hazardous when inhaled into the lungs, as they cause Legionnaires Disease (Legionellosis).
Legionella can occur when water systems in a building become contaminated with the bacteria (which breed in warm conditions) and then the contaminated water is sprayed to create a mist (with living bacteria within the droplets).
The risk of Legionella in church buildings and manses is very low and largely depends on how water is supplied to your building, how the water is stored and how the water is heated and distributed to your taps, toilets and, in some cases, showers and air conditioning systems.
HSE has updated their guidance, stating that even water supplied directly from the mains water supply may pose a small risk of transmitting legionella.
Legionella risk assessment
Current regulations require the duty holder to make a suitable and sufficient assessment of the risks from any work liable to expose employees to any substance hazardous to health before that work is carried out. Employers are also required to assess the risks to non-employees who may be affected by the exposure. They are also required to regularly review the risk assessment and make any necessary changes as a result of the review.
The risk assessment should include:
- Management responsibilities, including the name of the competent person and a description of your system
- Competence and training of key personnel
- Any identified potential risk sources, e.g. water storage tanks
- Any means of preventing the risk or controls in place to control risks
- Monitoring, inspection and maintenance procedures
- Records of the monitoring results and inspection checks carried out
- Arrangements to review the risk assessment regularly, particularly when there is reason to suspect it is no longer valid.
If it is concluded that there is no reasonably foreseeable risk or the legionella risks are low and are being properly managed to comply with the law, your assessment is complete.
You do not need to take any further action at this stage, but any existing controls must be maintained and the assessment reviewed regularly in case anything changes or is added to your water system.
Temporary building closure
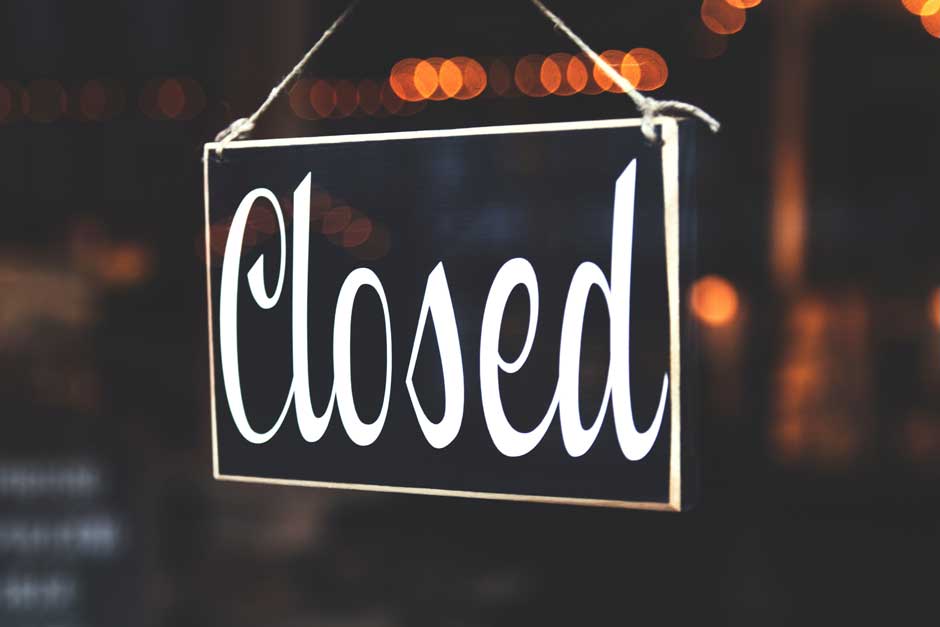
It is recommended that the planned water management inspections continue even during temporary closure of the building(s) as this is when stagnation in the water system is most likely to occur.
During temporary or prolonged periods of closure, we recommended that three basic control measures are taken during the routine weekly inspection of the building to minimise stagnation and any build-up of bacteria within the water system even if the perceived risk of legionella is considered low in your building(s).
- All taps and showers should be run for two continuous minutes at least once a week
- Hot water should reach a temperature of at least 500C
- Cold water should be below 200C
A record of any water checks should be recorded and kept as part of the water management plan for your building(s) if required.
Water management in buildings with a possible risk of legionella
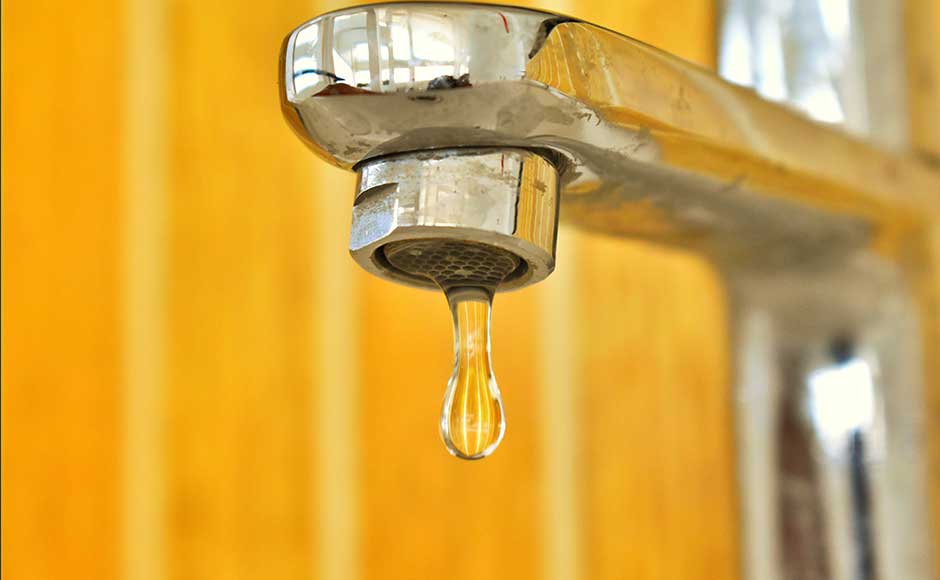
The congregation’s appointed Health and Safety representative(s) should ensure that there is a water management plan if they have identified the possible risk of legionella in your building(s).
A Water Management Risk Assessment should also be carried out if your building is considered at risk of legionella.
The appointed Health and Safety Representative(s) may be competent to carry out the assessment in-house but, if not, they should call on help and advice from the General Trustees Health and Safety Department or from outside sources, such as water treatment consultancies.
The person(s) responsible for managing legionella risks must understand water systems; the equipment associated with the fitted system such as water storage tanks, pumps, heat exchangers, showers etc, and its constituent parts; and identify whether they are likely to create a risk from exposure to legionella and whether or how:
- The water temperature in all or some parts of the system is between 20–45 °C
- The water storage and re-circulation process works
- There are sources of nutrients such as rust, sludge, scale, organic matter and biofilms (these conditions are likely to encourage bacteria to multiply and are often found in elevated water storage tanks)
- It is possible for water droplets to be produced and, if so, whether they can be dispersed over a wide area, e.g. showers, hoses and aerosols from air conditioning units
- It is likely that any of your employees, congregation or visitors etc are more susceptible to infection due to age, illness, a weakened immune system etc and whether they could be exposed to any contaminated water droplets.
Water services
Irrespective of any statutory responsibility, Charity Trustees should ensure that any premises for which they are responsible are in as safe a condition as is reasonably practicable. It is sensible to let water run for a period from taps which have not been used for a while.
Procedures to be followed if any premises are to be occupied after a period of vacancy:
- The incoming main water supply pipe should be examined and any lead pipework be replaced in accordance with water supply by-laws (local authority grants may be available for this work)
- Distribution pipework within the building should be examined and any lead pipework replaced with copper or other approved materials
- The water storage tank(s) should be examined, drained, cleaned, disinfected, and flushed out. The tank(s) should be fitted with proper ventilated covers in accordance with water supply by-laws.